サイト内の現在位置
個別受注生産型製造業向け
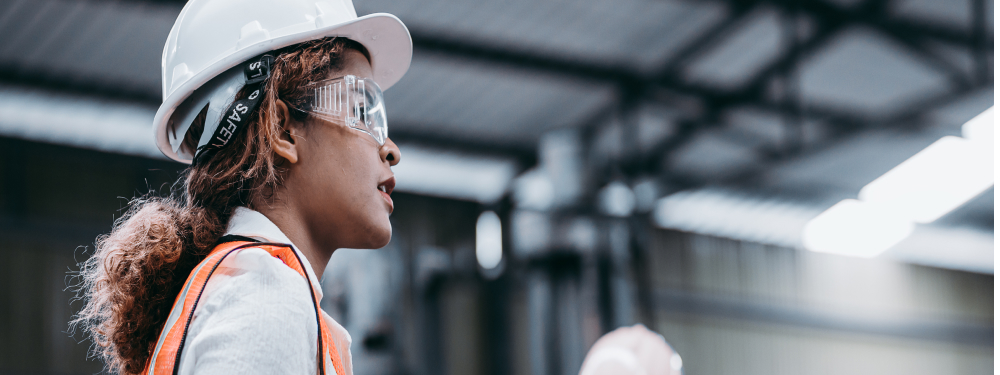
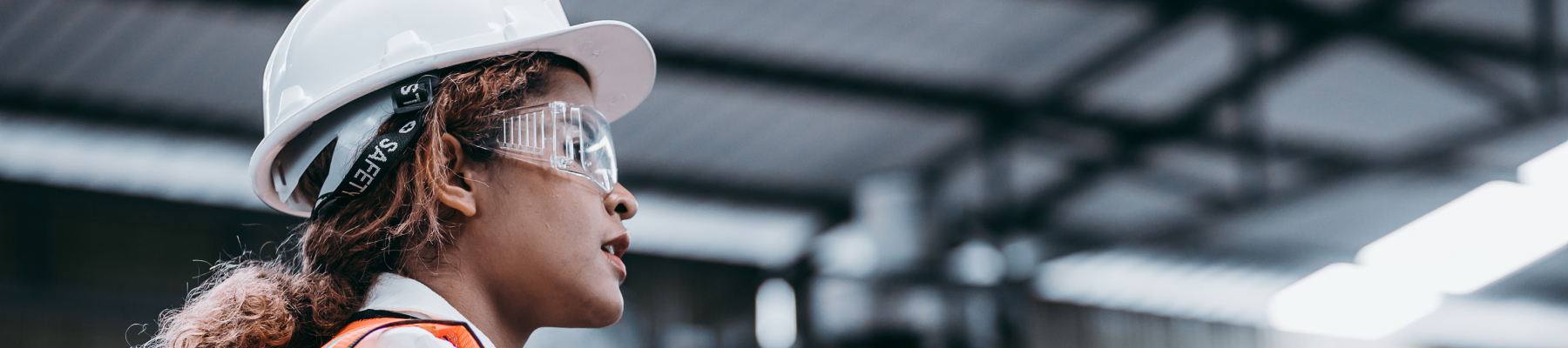
このようなお悩みはございませんか?
- 納期・仕様が決まらずにリードタイムが長期化してしまう
- 目標原価に対し実績原価がオーバーしてしまう
- コスト、進捗を可視化し適切な対策をとりたい
NECネクサソリューションズは個別受注生産型製造業全体を支援するソリューションを用意しています
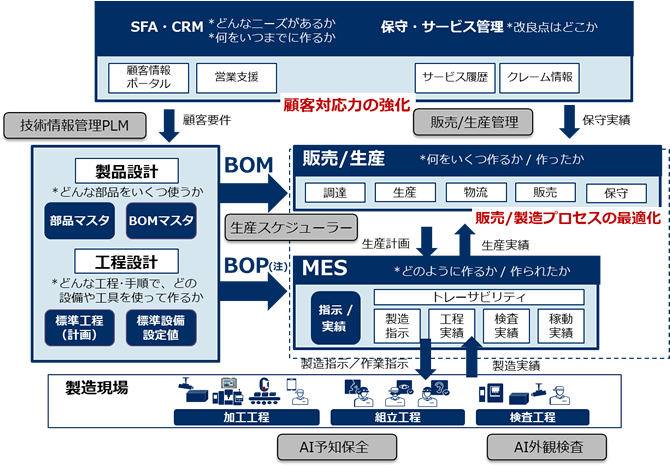
個別受注製造業の更なる成長に向けて
-NECネクサソリューションズがオススメしたいこと-
1.変動対応力の強化
個別受注生産型製造業では、顧客からの仕様変更や見直しが多いことはいわば“宿命”になっており、設計から生産までの全工程にわたり顧客の要件変動に対する柔軟かつ迅速な対応が求められております。
そのためには、全体最適な計画立案を行うことが重要です。
個別最適 | 各部門が個別最適な計画を立案すると、工程間のリソースの不整合が発生しやすくなり、顧客納期に応じた生産ができない |
---|---|
全体最適 | 各部門間の状況共有と情報の一元化を行い全体最適な計画立案を行うことにより、顧客納期に応じた生産が可能 |
必要な施策
- 営業の見込み情報を共有し、在庫情報を加味しながら販売/生産計画を立案する。
- 営業が案件登録、設計申請をした段階ですぐに設計が開始できるようにし、設計部門が五月雨出図をしたら部品手配ができるようにする。
- 共通品と個別設計品を区分けしキーパーツを明確にした上で、長納期品等は生産計画上不整合が生じないタイミングで先行手配をする。
- 顧客の要求仕様に変更が発生した場合はすぐに設計部門に情報を受け渡し、仕様の食い違い/漏れが生じないようにする。
- 設計変更の内容、理由、影響範囲をタイムリーに伝達し、生産部門側で仕掛も含めた適用可否判断ができるようにする。
- モノを識別する基準となる部品表を各業務毎に整備し、統合管理(設計BOM、生産BOM、保守BOM等)することで、伝達ミス/漏れが発生しないようにする。
- 流用設計/生産を推進して個別設計品の割合を少なくし、納期、コスト、品質のバラツキを極力抑える。
2.コストと進捗の見える化
精度の高い目標原価算出のために
設計、生産における精度の高い目標原価の管理を実現するためには、製品コストの実績値の見える化が重要なポイントになります。
例えば、設計段階において、代替品も含めた部品の調達/製造コストがわかると、よりコスト面で有利な部品を採用することができ、製品コストを下げることができます。
また、目標コストと実績コストの乖離がある場合、費目単位で分析をすることにより、設計上の問題か作り方の問題か対策ポイントが絞りやすくなります。
正確な実績原価算出と進捗の見える化実現のために
一方、設計、生産段階で正確なコストを集計するためにはタイムリーな実績収集が必須になります。
もし工程設計の段階で工程単位にコスト試算をしても、同じ単位で実績をとらないと差異分析ができません。 タブレット等を活用し、図面や作業手順書の電子化を図るとともに、作業実績、品質記録のリアルタイムな登録を推進する等の仕組みも有効です。
また、各部門で、常に引き合い~設計~生産~出荷までのプロジェクトの進捗を可視化、共有することで、早い段階での納期遅延、コストオーバーに対するリカバリー対策がとりやすくなると同時に、適切なタイミングで作業や事前準備に取り掛かることができます。
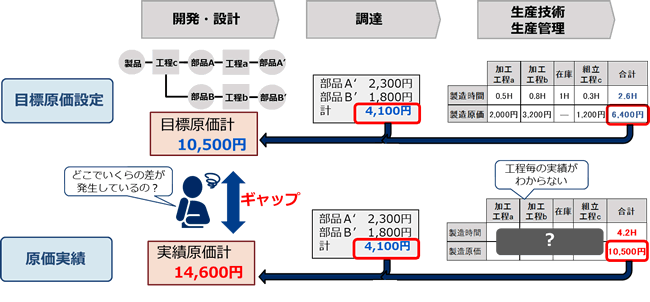
この課題を実現するソリューション
個別受注生産型製造業向け基幹業務パッケージ
「EXPLANNER/NX」(エクスプランナー・エヌエックス)
販売、債権、債務、会計、生産、原価。基幹業務の中核となる経営基盤を提供。業種・業務ごとのコンポーネントを組み合わせ、要件にピッタリなERPシステムを構築します。
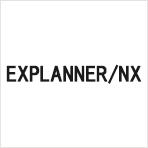
Web型ERPソリューション「GRANDIT(グランディット)」
グローバル化・多様化・スピード化が進むビジネス社会、企業間・組織間・個人間でのノウハウ・情報の共有、そして相互の連携と交換による「協創」。
GRANDITはコラボレーションの場を提供します。
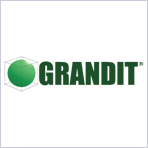
PLMソリューション「Obbligato(オブリガート)」
図面や部品表などの製品コンテンツを製品ライフサイクル全体に渡ってコントロールし、製品の早期市場投入を実現します。
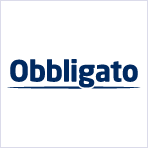
生産スケジューラ「Asprova(アスプローバ)」
多品種多工程の生産計画を超高速に作成します。機械や人員の負荷を考慮しながら、工場の中の一台一台の機械や一人一人の人員のスケジュールを秒単位の精度で作成し、実行可能な作業指示データを出力します。
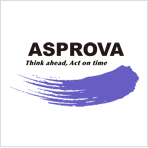
お問い合わせ・ダウンロード